SUMMARIZED FROM THE BOOK:
“HOW TO BUILD AND MODIFY ROCHESTER QUADRAJET CARBURETORS”
BY CLIFF RUGGLES
The Rochester Quadrajet was a standard production four-barrel carburetor used by every General Motors division for nearly 20 years. Although it never deviated far from its original basic design, the Quadrajet underwent several modifications over the years, proving its versatility over a wide variety of applications. From a practical standpoint, most Quadrajets were never intended to be “high-performance” carburetors. General Motors produced vehicles for a very broad customer base, and each division developed its own engines. Since many different engines were offered in a wide variety of vehicles, nearly every carburetor was calibrated for the specific application. With ever-increasing federal emission standards, manufacturers were forced into making their engines as efficient as possible, which led to future changes.To better understand the Quadrajet, we must start right from the beginning.
The Rochester Products division of General Motors was located in Rochester, New York, and had built single and multiple-bore carburetors for GM vehicles since 1949. Rochester’s 4-barrel casting known as the 4G had been one of GM’s standard production carburetors, but as economy and emissions concerns grew, Rochester responded with an entirely new 4-barrel carburetor, the Quadrajet. It boasted small primary bores for maximum throttle response and fuel efficiency, and larger secondary bores to meet the overall flow demands under full-throttle conditions.
The Quadrajet was designated the 4M series. This would be the basic casting from which all future variations evolved. Chevrolet was the first and only GM manufacturer to use the 4M Quadrajet in 1965. The 4G 4-barrel, however, was used on other Chevrolet V-8 applications, while radical, high-performance applications retained the Holley 4-barrel.
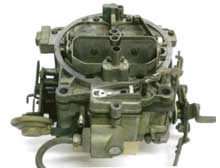
Shown here is a 1966 Quadrajet, carburetor number 7026260. This basic design was typical of very early production carburetors. Carburetors produced in later years would appear similar externally, but many internal changes were made to make them more reliable.
The Quadrajet saw expanded use onto a wide variety of 1966 Chevrolet V-8 and Buick 400 and 425 V-8 cubic-inch engines in 1966. Oldsmobile followed suit. By 1967 Cadillac and Pontiac too had begun installing the Quadrajet on most of their 4-barrel applications. With its growing popularity and efficient design, the Quadrajet was the most widely used production 4-barrel carburetor on GM-produced engines during that time. And though other carburetors such as the Rochester 4G, the Carter AFB, and the Holley 4-barrel were used on certain engines, the Quadrajet quickly became a benchmark for other 4-barrel carburetor manufacturers.
The 1968 model year marked the first nationwide federal standards for specific pollutants. And because of its efficiency and excellent balance of economy and performance, the 4M Quadrajet became the standard production 4-barrel carburetor for all GM manufacturers. The Rochester 4Gwas phased out as the Quadrajet replaced everything except the Holley 4-barrel, which continued on certain Chevrolet applications through 1972.
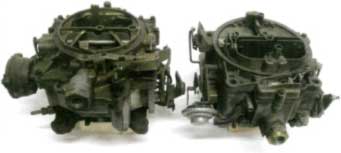
The carburetor on the left is a Rochester 4GC, used widely by General Motors until the Quadrajet (shown on the right) was introduced.
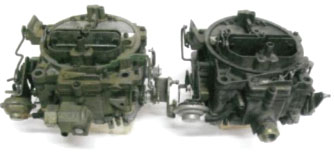
One of the first major changes to the Quadrajet design was making it available in both front- and side-inlet models, shown here. The front inlet is shown on the right; side inlet is on the left.
With the Quadrajet used by all GM divisions, each manufacturer required certain characteristics that matched its under-hood routings. The most common difference is the forward-facing fuel inlet as opposed to those that are side facing.
The Quadrajet was used on such a wide variety of engine sizes from each respective automobile manufacturer, that separate fuel-metering circuits and a variety of vacuum sources were also required and each carburetor was given a specific casting number. The product identification numbers were stamped into a circular disc located on the driver’s side of the main body up to the 1968 model year. Demand from the divisions had increased to the point that Rochester could not meet the volume requirements.
To prevent production delays, GM approached the Carter Corporation about producing Quadrajets in addition to Rochester. The Carter-built units are nearly identical to the Rochester-produced Quadrajet. The only differentiating characteristic is “Quadrajet by Carter” cast in place of“Quadrajet by Rochester” on the side of the main body. Since Carter produced Quadrajets well into the 1970s, they are not necessarily uncommon. Either would make an acceptable starting point for performance modifications……
Not unlike anything designed from a clean slate, the early Quadrajets were plagued by several small problems, such as the plunger-style fuel valve and the secondary-air-valve dash-pot assemblies. These were improved upon in subsequent years. The first notable changes occurred for the 1969 model year.
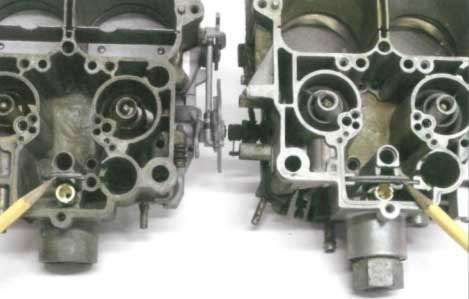
Moving the float fulcrum forward for 1969 (carburetor on right) models was one of the first
major design changes for the Quadrajet. The early-style float arrangement continued in
production well into the 1970s for various applications.
A smaller float with a relocated fulcrum increased float-bowl volume and provided more pressure on the fuel needle to better control the fuel level. Though these types of changes were typically implemented in all the Quadrajets produced, the Oldsmobile and marine applications retained the earlier-style float for several years
Another series of changes occurred in 1971. Plastic caps were placed over the idle mixture screws on the base plate of certain Quadrajets. These were used to limit travel and prevent grossly inaccurate adjustments, which could affect emissions. Internal metering changes were also required, with General Motors implementing a maximum compression ratio of just 8.5:1, which applied to each division for the 1971 model year. This was not only an attempt at reducing emissions, but also allowed the engines to operate on low-lead or unleaded fuels. The federal government imposed limits on the amount of lead in fuel. Eventually it was removed entirely. Leaded gasoline had been available for several decades prior. The lead was added in an attempt to increase the overall octane rating of the fuel but was later found to also improve the life of the exhaust valve seats.
Since lead does not burn, it typically left behind a powdery residue, which coated the entire combustion chamber, including the exhaust valve and exhaust valve seat as the gasses exited. When lead was removed, the extreme heat of the exhaust gasses passing over the valve seat and the rotating action of the valve itself generally wore untreated cast-iron seats more quickly, especially with an engine that was frequently under heavy load. It was determined that the lead acted as a “lubricant,” preventing direct contact between the valve seat and the valve and reducing the wear process.
Shortly after lead restrictions were enacted, many GM divisions began taking measures to reduce wear by induction-hardening the exhaust-valve seats on their cylinder heads. This process incorporates heating the valve seat to approximately 1800 degrees F for a short time with a coiled wire fixture. As the seat cooled, the result was an electrically inducted, hardened seat that extended about .050-inch below the surface. This greatly increased exhaust valve seat life and improved engine performance.
The compression ratio loss took its toll, but performance was still strong from all the GM manufacturers. While the others may have approached improving lower-compression performance in a different manner, Pontiac and Buick both compensated by addressing the Quadrajet.
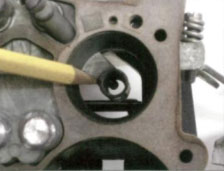
In 1971 Pontiac used a special version of the Quadrajet lacking the outer booster rings. The idea was to provide additional airflow, but these carburetors lacked the part-throttle efficiency of standard units and were difficult to get through emission testing. They were discontinued by the 1972 model year.
The 1971 Pontiac HO carburetors, lacking the outer booster rings, were actually special castings. Shown here is the bottom of the single booster extending well into the main primary bore.
The 1971 Pontiac HO carburetors, lacking the outer booster rings, were actually special castings. Shown here is the bottom of the single booster extending well into the main primary bore.
Pontiac modified the basic 4M Quadrajet casting by removing the outer velocity boosters that typically surround the discharge nozzles located in the center of the primary bore in the main body. A former Pontiac engineer noted that this significantly increased the airflow capacity of the carburetor and improved performance. But because of the weaker vacuum signal from the missing boosters, throttle response was degraded slightly, making them more difficult to tune and pass off-idle and low-speed emissions standards. The design was used for just one year. Five different casting numbers exist from 1971 Pontiac applications. They include Quadrajet numbers 7041267, 7041268, 7041270, and 7041273, which are specific to 455 HO engines, and Quadrajet number 7041263, which was used on 400 and 455 cubic inch engines with manual transmission. These are extremely rare and highly coveted by the Pontiac crowd. These particular carburetors were more than just stock castings with the outer booster rings removed. The outer booster rings were redesigned to extend almost 1 inch further into the main venturi area…….
in 1971 Buick improved the performance of its large-displacement engines by increasing the airflow capacity of its Quadrajets. Rather than expanding on Pontiac’s approach, they simply enlarged the primary bore in the main body. Typically 1 3/32 inches in diameter, Buick’s modifications increased bore diameter to 1 7/32 inches. Generally referred to by airflow capacity of “approximately 800 cfm,” Buick continued using this design through 1974. Its advantage of additional airflow improved performance, but unlike Pontiac’s approach, Buick’s Quadrajet retained the velocity boosters for maximum throttle response and improved emissions.
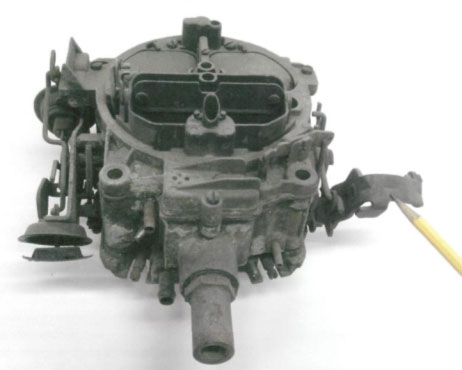
Here’s a great salvage-yard find, a 1971 Buick carburetor. These carburetors were the first large primary bore castings, often referred to as “800 cfm” carburetors. They are easily identified by the slashed front vent tube and long curved arm on the throttle linkage
These early Buick carbs are an excellent starting point for a high-performance carburetor and are the only large CFM castings produced with divorced-style chokes.
Plastic limiter caps were installed onto the idle mixture screws of all Rochester carburetors for 1972. That year saw another major step in the reduction of exhaust emissions with the introduction of an exhaust gas recirculation (EGR) valve onto certain Buick applications. All GM divisions used the EGR system extensively that year. A typical system consisted of a vacuum-actuated valve mounted on the intake manifold. The valve allowed exhaust gas passing through the exhaust crossover to circulate back into the intake plenum, where it would intermix with the incoming mixture of fuel and air. Since the production of NOx is directly related to combustion temperatures, the exhaust gas actually cooled the combustion chamber, reducing the amount of NOx under light load. To maximize the effects of the EGR system, the primary circuits of Quadrajets destined for EGR applications was slightly leaner.
Since exhaust gas is inert, it does not burn under normal combustion, and in theory it occupies volume normally occupied by the combustible air/fuel mixture. And with less combustible air in the chamber, less fuel is required. With less combustible mixture, flame intensity cannot be as great, which reduces combustion temperature and the production of NOx.
The vacuum source for the EGR valve was a specific vacuum port located in any number of places on the Quadrajet main body or base plate.
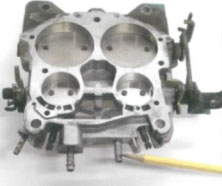
Many Quadrajets have special vacuum source locations specifically designed for EGR valve operation. Shown here is a 1974 Pontiac base plate noting the EGR port.
Since EGR could cause a slight hesitation just off idle or a lean surge when decelerating, the EGR valve was only active at part-throttle cruise. The EGR-specific vacuum port reflected these requirements. A special timed port provided varying amounts of vacuum that increased proportionally with throttle angle to meter the varying amounts of exhaust gas that recirculated into the intake manifold. Because of its unique vacuum signal, the EGR vacuum port makes neither an acceptable ported nor manifold vacuum source. The high source location in the base plate does not provide a strong enough signal right off idle to effectively operate the distributor vacuum advance. Pontiac engineers used a variation of Buick’s large-bore carburetor on its potent Super Duty 455 in 73-74. These high-performance carburetors are among the best for modification…….
The large-bore Pontiac carburetors have a carburetor-mounted thermostatic coil assembly on the main body. Buick’s model received a manifold-mounted thermostatic choke coil. Both of these Quadrajets are considered the best of the 4M-series for high-performance use. Since the Super Duty carburetors used the hot-air-style choke, the choke pull-off was moved to a separate bracket bolted to the front of the carburetor. The 4M casting was redesigned for 1975 and is referred to in Delco literature as the “Modified Quadrajet” and designated the M4M series. Most retained the larger 1 7/32 inch primary bore like the Buick and Super Duty Pontiac 4M, though some castings bound for low-performance, small-displacement applications retained the 1 3/32 inch bore.
Regardless, the new modified castings also included several design changes. The most notable was a much smaller float design. This increased fuel-bowl capacity while maintaining sufficient pressure on the needle/seat assembly to control fuel level. Other changes included an adjustable part throttle (APT) system located in the right front corner of the main body.
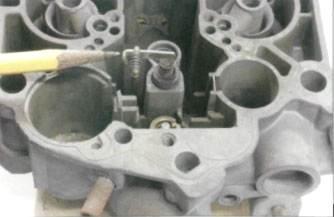
Some 1975-76 models used an auxiliary power piston with a single metering rod
and pressed-in jet. This system worked in conjunction with the APT system and
the main jets and metering rods
A brass cap in the air horn was located directly above an adjustment screw and was used to fine-tune part-throttle air/fuel mixture ratios.
In addition to APT, many 1975 model-year Quadrajets received an additional power piston and single jet/rod assembly. The intention was to provide closer control over the air/fuel ratios while operating on the primary circuit. However, this was not as effective as initially desired and was removed from most carburetors by the 1976 model year. The carburetors using the auxiliary power piston assembly are somewhat difficult to set up for performance use. Although they can be modified with some additional effort, it is usually better to simply obtain a later-style carb.
The 1976 castings are the first of the more desirable M4M Quadrajets. They contain many features that make them an excellent starting point for high-performance use. With an external appearance identical to the 1975 castings, they too use the small float design. The APT system, however, was relocated next to the primary power piston in the void left from the auxiliary power piston that was used in 1975. A black plastic cup filled the cavity left from the 75-type APT.
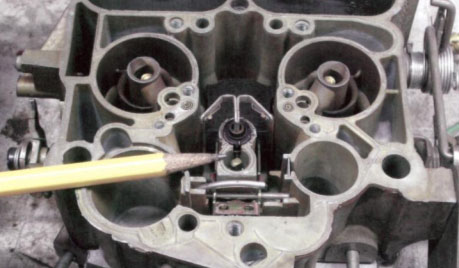
This later APT system replaced the single pressed-in jet and metering rod used in the 1975 and some 1976 models. The new system had a provision to raise and lower the power piston.
The power piston was equipped with a small pin that contacted the APT adjustment screw, which could be adjusted externally. This new-type APT system allowed for full control over part-throttle air/fuel ratios by simply repositioning the tapered portion of primary rod in the primary jet. Because of this flexibility, these carburetors are much easier to tune than earlier units. The Quadrajet continued for the rest of the 1970s without any significant changes. In 1979, however, the plastic limiting caps on the idle mixture screws on Quadrajets were eliminated. Hardened steel caps pressed into the base plate took their place. This made any additional tuning impossible and prevented any adjustment that could affect tailpipe emissions. Several methods of removing these plugs have evolved over the years, but the most effective method was printed in AC Delco service literature. A Center punch and a sharp hacksaw blade are used to score and cut the front edge of the base plate. The main drawback is the rough cutting marks left behind on those that have had the steel plugs removed. Once removed, however, these base plates are as good as any other.
The start of the 1980 model year was virtually a carryover from the previous year. One noticeable change was the Quadrajet choke system. The screws that typically fastened the thermostatic choke coil to its housing were replaced by rivets. This was another attempt for better control of emissions by removing the chance of an incorrect choke valve adjustment……
One of the most significant changes made to the Quadrajet since the inception of its original design occurred during the 1980 model year. With the introduction of Computer Command Control (CCC) on several GM vehicles, the Quadrajet was redesigned to accept electronic internal components, which offered more precise control over main-metering-system-reducing emissions and improving economy at part throttle. This latest version of the basic Quadrajet was given a model designation of E4M, which signified an Electronic Controlled 4M carburetor. The secondary circuit, however, was not affected and operated conventionally. The heart of the CCC system was an Electronic Control Module (ECM), which monitored several engine parameters under normal operating conditions. An oxygen sensor in the exhaust stream Quadrajets started showing up in the 1980s with electronic mixture-control and an electronic throttle position sensor solenoids (left, blue) and throttle-position sensors. within the main body of the carburetor sent electronic signals to the ECM. Based on the input, the ECM sent varying signals to an electronic mixture-control solenoid within the carburetor, which controlled the depth of the primary metering rods in their jets, richening or leaning the mixture based on engine load.
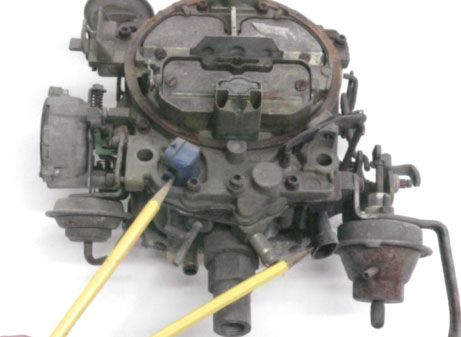
Quadrajets and ECM
This procedure replaced the vacuum-sensitive primary power piston and APT system in the conventional M4M series Quadrajet. A variation of this design retained the conventional power piston but contained an electronic mixture-control solenoid that controlled part-throttle mixture with a 75-type APT.
The E4M Quadrajets were not necessarily problematic, but they can be very-difficult to calibrate for performance applications that do not use an ECM and all related equipment. The primary bore was typically 1 3/32 inches and they were calibrated for low-performance, small-displacement engines where economy and emissions were of the utmost concern. And because of this, finding larger primary jets and smaller primary rods for performance applications can be very difficult. They can make an excellent donor to salvage parts from since so many parts interchange with other 4M and M4M Quadrajets. However, once the electronic equipment is removed and modi- fied correctly, the E4Ms make excellent performance carburetors. The M4M Quadrajet was used extensively by all GM divisions.
Remarkably, they were even installed on smaller-displacement engines such Chevrolet’s 305 ci and Pontiac’s 301 ci. This just proves how versatile the Quadrajet is – the same basic casting can be found on a wide array of GM engines with displacement ranging from as little as the 300ci engines from Chevrolet, Oldsmobile, and Pontiac, to Cadillac’s enormous 500ci mill. Regardless of its original application, any Quadrajet can be modified to fit the needs of another application.